What is Six Sigma and How Can it Help with Capacity Building of a Quality Environment in My Organization?
- crosqblog
- on Nov, 19, 2019
- Category Demand for Quality
- Comments Off on What is Six Sigma and How Can it Help with Capacity Building of a Quality Environment in My Organization?
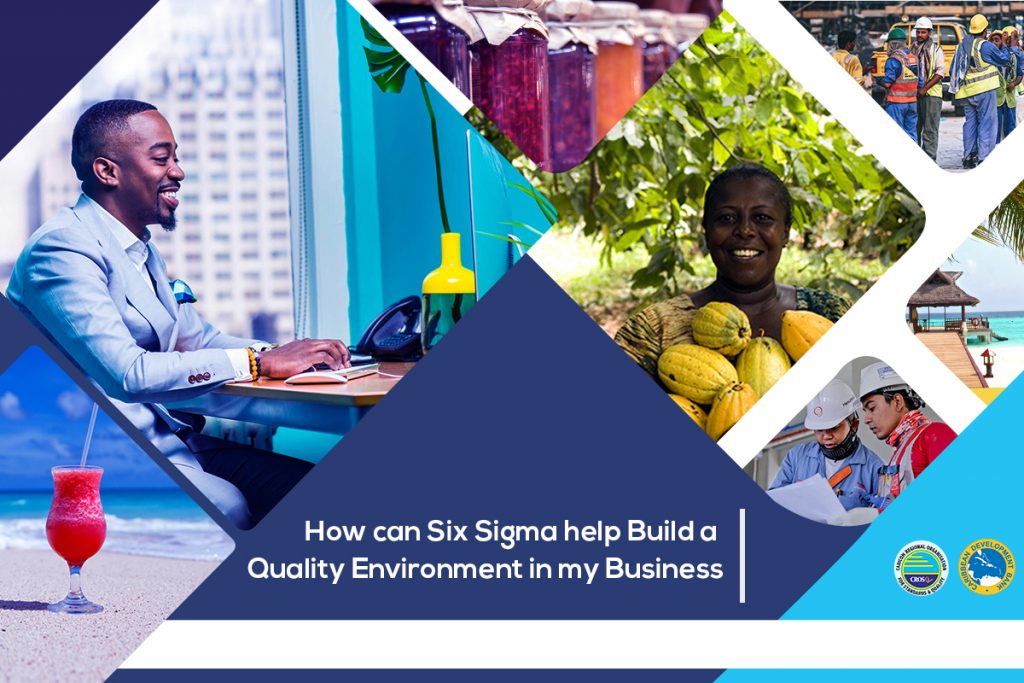
Six Sigma is a quality assurance strategy used by many leading global companies such as Amazon, the Ford Motor Company and Dell. It is called Six Sigma because of the strategy’s heavy dependence on statistical tools. The name refers to six standard deviations between average and acceptable limits based on the bell shaped curve.
A company that provides Six Sigma quality guarantees that its internal processes are well controlled. The data-driven component of Six Sigma involves the use of various statistical tools which require special training. Consideration to this fact should be taken when embarking on the implementation of Six Sigma in your organisation.
The aim of Six Sigma is to “reduce process defects to 3.4 per one million opportunities”. There are three Six Sigma methodologies: DMAIC, DMADV and DMEDI. There is also a new school of thought centering on the concept of Lean Six Sigma.
The DMAIC Methodology
This methodology is most suitable for existing manufacturing and production processes. It has five stages:
- Define: The processes that will be examined should be named and understood by those involved.
- Measure: Relevant measurements should be taken to effectively assess the business process. Quantitative measurements, when done correctly, eliminate bias. Note any defects that are observed.
- Analyse: Assess the data to determine probable causes for the defects. Identify gaps.
- Improve: Execute a plan to improve the process.
- Control: Prevent regression into the old way of doing things and keep the business on track for growth.
The DMADV Methodology
This methodology is most suitable for customer relations and the development of a new product or service. It has five stages:
- Define: Identify the purpose of the project and set realistic, measurable goals based on customer requirements.
- Measure: Measure customer’s Critical to Quality (CTQ) requirements and refine existing goals to meet them.
- Analyse: Assess the measurements and determine the actions that should be taken.
- Design: Create a model that clearly demonstrates the chosen alternative.
- Verify: Test the model on customers and decide whether it should be used in the long-term or revamped.
The DMEDI Methodology
This methodology is typically used for managing specific projects within an organisation and may be the best Six Sigma methodology for small businesses. It has five stages:
- Define: Everyone involved in the project should know its nature and scope, internal and external customers, and financial benefits.
- Measure: Determine how each element of the project will be measured to establish its success. These measurements should be a part of the goals that are set so that the goals are quantifiable.
- Explore: Identify new ways to approach a project. There may be some things that the organisation has historically done wrong and these faux pas should be considered before delving into the project.
- Develop: Create a strong plan to meet the objectives outlined for the selected alternative. The plan should include the human and non-human resources that are needed for successful project execution.
- Implement: Carry out the plan.
The Lean Six Sigma Concept
ASQ’s definition of Lean Six Sigma is provided below.
Lean Six Sigma is a fact-based, data-driven philosophy of improvement that values defect prevention over defect detection. It drives customer satisfaction and bottom-line results by reducing variation, waste, and cycle time, while promoting the use of work standardization and flow, thereby creating a competitive advantage. It applies anywhere variation and waste exist, and every employee should be involved.
It is the highest level of continuous improvement because it merges two of the best process improvement concepts in the world: Lean and Six Sigma. The aim is to create a culture of always pursuing improvement at the highest level within the organisation. A lean strategy involves the use of the PDCA methods and tools such as 8 wastes and 5S to achieve continuous improvement.
The “PDCA is a four-step problem solving method for continuous process improvement”. The four steps are:
- Plan: Visualise the root cause of the problems within the organisation and create a plan to address the issue.
- Do: Apply countermeasures to fix the root problem.
- Check: Determine whether the problem has been fixed based on the established goals.
- Act/Adjust: Make changes to facilitate continuous improvement.
The 5S tool promotes an organised and safe workplace. It has five stages:
- Sort: Purge the workplace so that only necessary items remain.
- Set in Order: Place items in the correct order to create efficient workflow.
- Shine: Keep the work area clean.
- Standardise: Create and implement standards for all workers to maintain an organised workplace.
- Sustain: Continuously review the standards to identify areas that need improvement.
Waste removal is pivotal to the Lean Six Sigma process. The Lean process identifies eight categories of waste: defects, overproduction, waiting, non-utilised talent, transportation, inventory, motion and extra-processing. It is important for organisations to understand where resources are being wasted and stop it.
What is the Right Way to Implement Six Sigma in a Small Business?
It has been said that Six Sigma is best for businesses with 500 or more employees. However, Six Sigma can be modified for use in small businesses. This modification requires:
- Full support and guidance from the owner (the owner should take a hands-on approach)
- Specific processes within the business that would benefit otherwise it would be a waste of time and resources
- Tolerance for change and the factors that come along with it
- Availability of spare resources
- The right expertise and training
Capacity Building and Six Sigma
Capacity building can be defined as “the process of developing an organisation’s strength and sustainability.” The Six Sigma strategy you choose (DMAIC, DMADV or DMEDI) will determine the focus of your capacity building efforts.Your aim is to ensure that you are able to identify any gaps within the organisation and sufficiently address these gaps regardless of the method you choose.
Appointing what Six Sigma strategist’s call green belts helps streamline this process. Green belts are employees within the organisation who spend some of their time on Six Sigma projects. Small businesses cannot afford to have black belts who are wholly devoted to carrying out the Six sigma mandate. Your green belt team will be the Six Sigma champions within your organisation and help the rest of your team get on board with Six sigma quality.
Final Words
Six Sigma is an important consideration for organisations serious about continuously producing quality. Small businesses should only consider Six Sigma for the business processes that really need it. In fact, the best methodology for a small business owner to consider is Lean Six Sigma. The CEO of a small business also has to play a hands-on role in the planning and implementation of each Six Sigma element. Finally, green belts should be appointed within the organisation who spend some of their time ensuring that Six Sigma supports the organisation’s capacity building goals.